Compressive Strength Testing of Plastics
The compressive strength of a material is the compressive force per unit area that it can withstand. This is in contrast to the more commonly measured tensile strength. ASTM D695 is the standard test method in the USA. The figure below, from Quadrant Engineering Plastic Products, shows the test geometry.
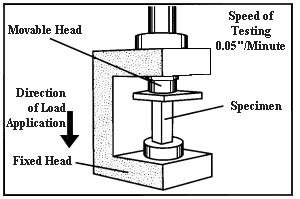 |
ASTM D695: Specimen of 1/2" x 1/2" x 1" is placed in the compression apparatus and a known load is applied. |
North American plastics manufacturers generally report compressive yield strength, the stress measured at the point of permanent yield, zero slope, on the stress-strain curve. Ultimate compressive strength is the stress required to rupture a specimen. Materials such as most plastics that do not rupture can have their results reported as the compressive strength
at a specific deformation such as 1%, 5%, or 10% of the test sample's original height.
The analogous test to measure compressive strength in the ISO system is ISO 604. The values reported in the ASTM D695 and ISO 604 tests seldom differ significantly and are often used interchangably in the early stages of the materials selection process. These tests also give the procedure to measure a material's compressive modulus (the ratio of stress to strain in compression).
The table below lists average compressive strengths and compressive moduli for some filled and unfilled polymers.
Typical Compressive Yield Strength and Compressive Modulus of Polymers
(A wide variation is possible between specific grades)
Polymer Type |
Compressive Yield Strength (MPa) |
Compressive Modulus (GPa) |
ABS |
65 |
2.5 |
ABS + 30% Glass Fiber |
120 |
8 |
Acetal Copolymer |
65 |
2.5 |
Acetal Copolymer + 30% Glass Fiber |
100 |
7.5 |
Acrylic |
110 |
3 |
Nylon 6 |
50 |
2.3 |
Polyamide-Imide |
130 |
5 |
Polycarbonate |
70 |
2.0 |
Polyethylene, MDPE |
20 |
0.7 |
Polyethylene Terephthalate (PET) |
80 |
1 |
Polyimide |
150 |
2.5 |
Polyimide + Glass Fiber |
220 |
12 |
Polypropylene |
40 |
1.5 |
Polystyrene |
70 |
2.5 |
|
|