Izod Impact Strength Testing of Plastics
Several methods are used to measure the impact resistance of plastics - Izod, Charpy, Gardner, tensile impact, and many others. These impact tests allow designers to compare the relative impact resistance under controlled laboratory conditions and, consequently, are often used for material selection or quality control. However, these tests generally don't translate into explicit design parameters. The Izod impact test is the most common test in North America. The figure below, from Quadrant Engineering Plastic Products, depicts the Izod impact strength test apparatus.
ASTM D256: A pendulum swings on its track and strikes a notched, cantelevered plastic sample. The energy lost (required to break the sample) as the pedulum continues on its path is measured from the distance of its follow through. Sample thickness is usually 1/8 in. (3.2 mm) but may be up to 1/2 in. (12.3 mm). |
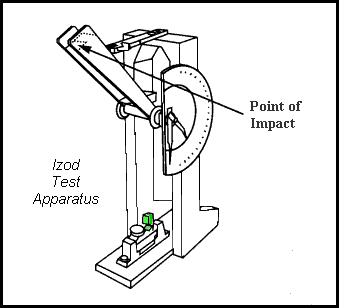 |
The test method generally utilized in North America is ASTM D256. The result of the Izod test is reported in energy lost per unit of specimen thickness (such as ft-lb/in or J/cm) at the notch ('t' in graphic at right). Additionally, the
results may be reported as energy lost per unit cross-sectional area at the notch (J/m or ft-lb/in). In Europe, ISO 180 methods are used and results reported based only on the cross-sectional area at the notch (J/m). |
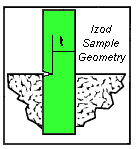 |
Polymeric materials that are sensitive to the stress concentrations at the notch ('notch-sensitive') will perform poorly in the notched izod test. Engineers use this knowledge to avoid using such polymers in designs with create high stress concentrations such as sharp corners or cutouts. Unnotched specimens are also frequently tested via the Izod impact method to give a more complete understanding of impact resistance.
Izod impact tests are commonly run at low temperatures - down to -40F (-40C) or occasionally lower - to help gauge the impact resistance of plastics used in cold environments.
The impact resistance of a given grade of polymer is a function of the base resin plus the presence of any impact modifiers (such as elastomers) and reinforcing agents that may be added by the manufacturer/compounder. Environmental factors, in additional to temperature, also play a role in impact resistance. For example, nylons (polyamides) generally experience higher impact strength in the conditioned state (in equilibrium with atmospheric moisture) than in a dry-as-molded state.
|